Offshore project: Upender and Gangway for Adwen
Offshore Company Adwen needed equipment to assemble a part of the JV8-170 or JV8-180 wind turbine, also known as MSA.
Initial situation description
This MSA is composed of two parts: the hollow shaft and the bearing housing structure.
Airpes was in charge of the design of the tilter and the gangway responsible for assembling the MSA parts.
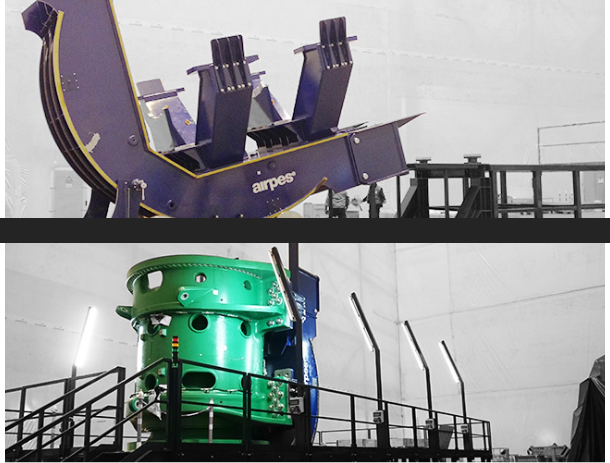
The MSA assembly process comes in two phases:
• Turning of the bearing housings
The bearing housings are supported on the upender’s structure horizontally, then vertically and finally the bearings are installed. It is removed from the tilter by a crane and re-installed horizontally and upside-down on the upender, at 180 °.
It is required to repeat the process to install the bearings on that side.
• Hollow shaft
The hollow shaft is installed horizontally and is lifted with the help of the upender at 90º. Finally, the bearing housing is inserted into the hollow shaft and assembled. At the end of these operations, it is necessary to return to the horizontal position to completely assemble the drive train.
OUR on demand solutions
Airpes Solutions
LATEST POSTS ON THE BLOG
Discover our brand new developments, events, get posted of our activity.
- Hoisting Weight LimitersHoisting weight limiters are critical for safe crane operations. Learn how they work, where to use them, and...
- 5S Lean Methodology for Industrial ExcellenceCrosby Airpes applies the 5S methodology internally to enhance safety, efficiency, and product quality. It's a key part...
- Wind Turbine Engineering: excellence in Blade InstallationCrosby Airpes applies the 5S methodology internally to enhance safety, efficiency, and product quality. It's a key part...
- Overhead Crane Parts: Complete Guide to Crane ComponentsHoists, rigging, sensors... What are the different components of an overhead crane? In this post we check it...